Understanding Reliable Air Compressors: Your Complete Guide
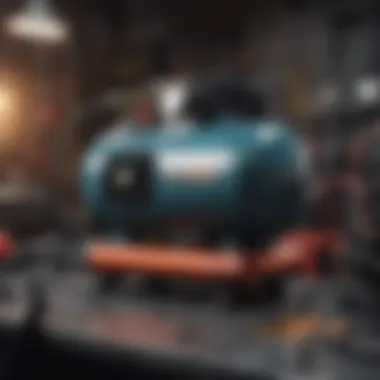
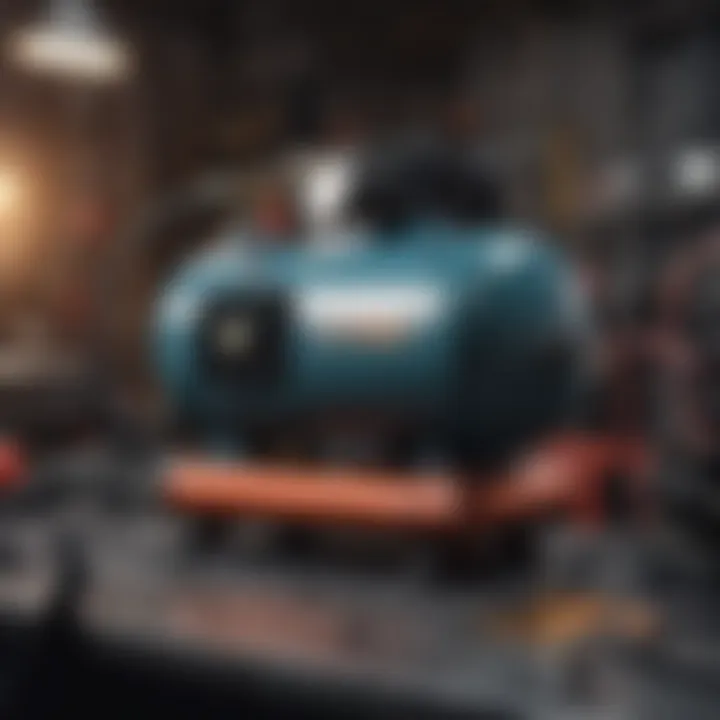
Intro
Understanding reliable air compressors is essential for professionals in various industries. The significance of air compressors spans across manufacturing, automotive, and construction sectors, where compressed air plays a vital role. Having a dependable air compressor not only ramifications for efficiency and productivity but also ensures safety and cost-effectiveness. In this comprehensive guide, we will examine types, features, applications, and maintenance tips, providing valuable information to help you make informed purchasing decisions.
Vehicle Review and Assessment
Overview of Specifications
A reliable air compressor should have clear specifications that meet your specific needs. Key specifications include pressure rating, tank size, and horsepower. Understanding these numbers is crucial for determining the best fit for an intended application.
Performance Metrics
Performance metrics reflect the compressor's ability to deliver consistent and powerful compressed air. You should consider the cubic feet per minute (CFM) the unit can provide, as well as its recovery time. The more efficient the performance metrics, the more reliable the machine is considered.
Interior Features and Comfort
While this section may seem out of place for air compressors, their usability can be increased through an efficient design. Notable features may consist of intuitive controls, portability options, and noise levels. Builders or operators will benefit from a quiet compressor that allows for comfortable long-term use without disrupting the working environment.
Safety Ratings and Features
Evaluating safety ratings is critical before purchasing an air compressor. Look for compressors that feature automatic shut-off systems, pressure relief valves, and thermal overload protection. These factors could significantly reduce the risk of accidents while operating.
Fuel Efficiency and Environmental Impact
In an age that demands sustainable practices, the fuel efficiency of an air compressor matters greatly. Gasoline-powered models should be carefully assessed for emissions standards and eco-friendliness. An energy-efficient air compressor not only reduces operational costs but also mitigates environmental impact like fuel consumption.
A dependable air compressor means your business runs smoother, ensuring minimal downtime on essential processes.
Key Considerations
When assessing compressors, it is worth considering warranty terms and durability. A longer warranty could indicate the manufacturerβs confidence in their product. Furthermore, reading user reviews or consuming testimonials can help gauge reliability as firsthand experience often provides insights beyond specifications
The End
Taking the time to assess and understand air compressors directly influences their long-term reliability. It's essential to familiarize yourself with metrics and specifications, focusing on aspects crucial to safety and efficiency. This guide aims to provide clarity in your search for the optimal air compressor.
Preface to Air Compressors
Air compressors play an essential role in numerous sectors, where they ensure the transformation of electrical or mechanical energy into compressed air. This process enables a wide array of applications, significantly enhancing functionality in many industries. Understanding air compressors helps one to make informed choices when selecting the right model for specific needs.
Definition of Air Compressors
An air compressor can be defined as a device designed to store and compress air in a controlled manner. It works on the principle of increasing the pressure of air by decreasing its volume. This is achieved through various mechanisms, leading to the classification of compressors renowned today. Notably, knowing this basic definition sets the foundation for understanding more complex functionalities and specificationsγ
Role of Air Compressors in Various Industries
Air compressors find applications in several key industries. For example, in the automotive field, they provide needed pressure for tire inflation and tools like impact wrenches. In the manufacturing sector, air compressors power pneumatic tools and assist in powering machinery requiring compressed air. Additionally, they are used extensively in construction, personal and industrial cleaning applications, and even artistic endeavors like spray painting.
A few key points regarding compressor roles in different sectors include:
- Automotive: Tire inflation, tool power, and paint application.
- Manufacturing: Pneumatic tools and instrument air systems.
- Construction: Jackhammers, nail guns, and hydraulic wedging tools.
- Cleanliness: Cleaning equipment for industrial machinery and garages.
Air compressors are indispensable for achieving efficiency and effectiveness in a variety of practical settings. Without them, tasks related to air pressure control would be difficult, time-consuming, and less effective.
Understanding how diverse industries leverage air compressors prepares the reader for deeper insights into the design and specifications of these vital devices.
Importance of Reliability in Air Compressors
Understanding the importance of reliability in air compressors is crucial for both users and manufacturers. Reliability in an air compressor signifies that the machine consistently performs its intended function without unexpected failures or inconveniences. This reliability directly contributes to efficient operations, minimizing downtime and ensuring that tasks are completed as scheduled.
The sound performance of an air compressor influences productivity across various industries. A reliable compressor not only keeps projects moving forward but also lessens operational issues that can arise during use.
Impact on Operational Efficiency
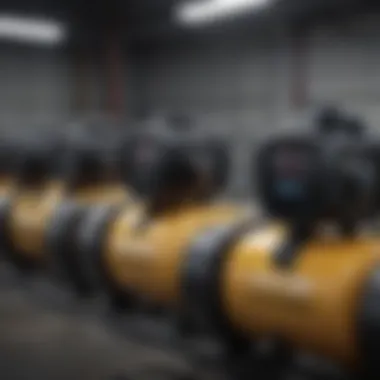
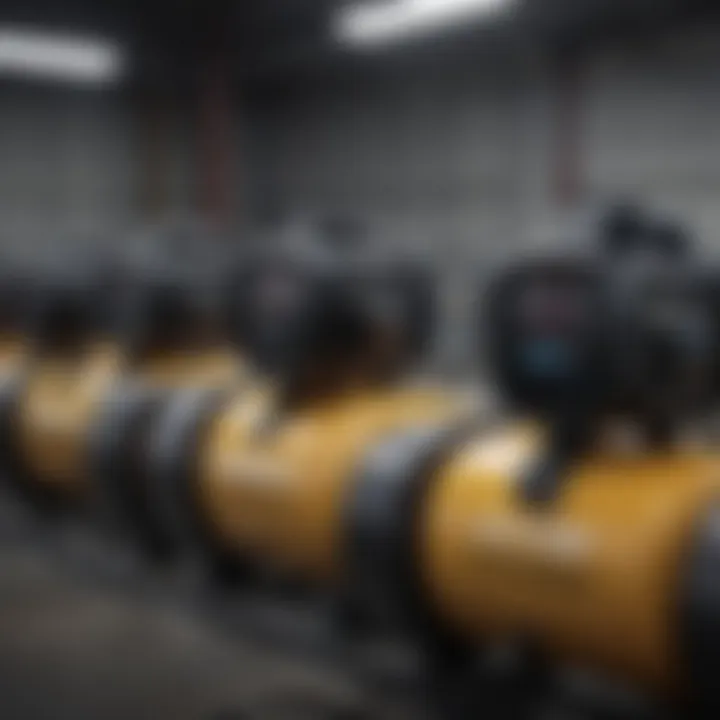
A reliable air compressor deeply affects operational efficiency. It acts as the backbone in many industries, from construction to automotive repair. When an air compressor functions optimally, it enhances the entire workflow. For example, if a compressor fails during an important project phase, it can disrupt timelines, delaying the completion of the work and potentially resulting in increased labor costs.
Moreover, regular, dependable performance helps businesses optimize their resource usage, resulting in better cost management. There are several factors tied directly to operational efficiency:
- Consistency: Workers can depend on the machine functioning correctly.
- Capacity: Reliable compressors maintain the desired pressure effectively.
- Less Frequent Breakdowns: This ultimately lowers repair costs.
In essence, a reliable air compressor supports the seamless execution of tasks, making it a worthwhile investment for maximizing productivity.
Cost Implications of Unreliable Compressors
While focusing on the immediate benefits of reliability, one should not overlook the costs associated with using unreliable compressors. Several potential expenses arise when an air compressore fails, including:
- Repair Costs: Regular breakdowns require equipment repair. This adds additional expenses promptly.
- Downtime: Time lost during repairs impacts production schedules, leading to potential financial losses.
- Operational Inefficiency: Unreliable machines can lead to improper yields or erroneous outputs, further complicating manufacturing processes.
As reported in various industry analyses, relying on low-quality or unreliable air compressors can produce expenses that far exceed the initial savings made during their purchase. Investing in a reliable air compressor pays off in the long run.
Types of Air Compressors
The realm of air compressors offers a variety of options, each designed for specific functionalities and performance levels. Understanding the different types of compressors is essential for selecting the most suitable one for your needs. Their features, efficiency, and operational principles affect everything from energy consumption to overall operation. By choosing the right type, one can optimize operations and enhance performance. Below, we delve into the main types of air compressors and what makes them distinct.
Positive Displacement Compressors
Positive displacement compressors are among the most widely used compressors due to their effectiveness and straightforward design. This type functions by trapping a fixed volume of air and then compressing that volume to a higher pressure. The process repeats, allowing for consistent and reliable air supply suitable for a variety of applications.
Two prominent examples of positive displacement compressors are:
- Reciprocating compressors, using pistons to compress air within cylinders.
- Rotary screw compressors, implementing two meshed screws to compress air continuously.
Advantages of positive displacement compressors include:
- High efficiency for most applications. (They offer optimal performance at varying discharge pressures.)
- Capable of producing high pressure. Many industries require these high pressures, making them crucial.
- Compact design, especially for reciprocating models, which on rare occasions can supply power for small spaces.
When deciding on a positive displacement compressor, consider the operational requirements and expected usage volumes. Having the right compressor can significanty influence productivity.
Dynamic Compressors
Dynamic compressors, also known as rotodynamic compressors, work quite differently as they incorporate a continuous process of air compression. Instead of trapping and compressing air, dynamic compressors impart velocity to the air and rapidly change its speed to create sustained pressure. Common types in this category are centrifugal and axial compressors.
Centrifugal compressors utilize a rotating impeller to increase air velocity. The kinetic energy enables dramatic changes in pressure. They are frequently used in:
- HVAC systems
- Automotive industry
Axial compressors are known for their application in larger setups, where volume and efficiency are integral. They filter air through a rotor in an axial fashion which allows better airflow for applications needing more than just high pressure.
Advantages of dynamic compressors include:
- Continuous air supply, making them suitable for high demand scenarios.
- Generally operate quieter than positive displacement types.
- Efficient for larger operations where space and power are considerations.
It is critical for industries to choose the correct compressor type. Choosing between positive and dynamic compressors ultimately revolves around operational needs and energy efficiency goals.
Key Features to Assess Reliability
Assessing the reliability of air compressors is crucial for any operation that relies heavily on consistent performance. The features of an air compressor directly correlate with its efficiency, durability, and overall functionality in real-world applications. Understanding these features helps buyers choose a compressor aligned with their specific requirements, reducing the risk of downtime and unexpected repairs.
Motor Power and Efficiency
The motor power of an air compressor relates directly to its capacity to perform workloads efficiently. A motor with sufficient power ensures that the compressor can generate the required airflow and pressure without strain. Efficiency is equally important. An efficient motor minimizes energy consumption while maximizing output, thus leading to cost savings. When evaluating motor power, buyers should review the specifications for horsepower and check for energy efficiency ratings.
Important Considerations:
- Loading and Unloading: The motor should manage holding pressure effectively, minimizing unnecessary energy use.
- Continuous vs. Intermittent Duty: Know if the usage will be constant or sporadic to choose a motor designed for such performance.
Tank Size and Design
Tank size plays a significant role in how well an air compressor delivers power over time. Larger tanks can store more compressed air, allowing for extended tool usage before needing to recharge. Additionally, the design of the tank can affect the dryer performance. A well-designed tank will facilitate better air recycling and minimize the moisture content within.
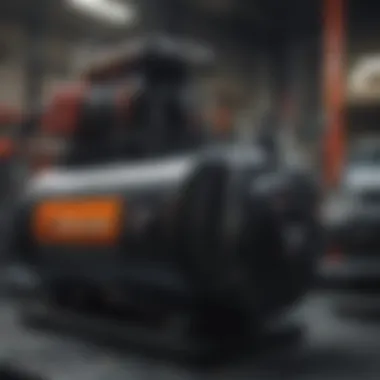
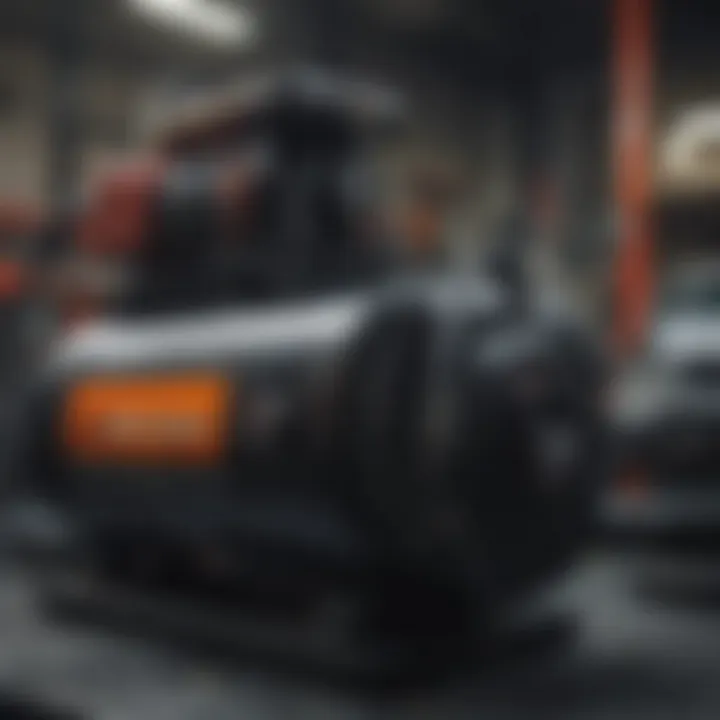
Key Factors to Review:
- Storage Capacity: Larger capacities offer more extended operation capabilities, essential for tough jobs.
- Portability: For non-stationary jobs, consider designs that foster easy mobility without compromising stability.
Pressure Control Systems
The pressure control system governs the compressor's operation, adjusting the speed based on demand and ensuring that optimal performance aligns with user requirements. This system is essential for maintaining the pressures needed for varied applications. High-quality systems employ advanced technology, which not only optimizes performance but also increases safety by automatically shutting down in excess pressure situations.
Essential Points:
- Adjustability: Selectable pressure settings can enhance the versatility for different tasks.
- Adjustment Mechanism: Verify if adjustments can be made quickly and easily.
Noise Levels and Operation
Noise levels in compressors matter, particularly in environments where sound disturbances can affect productivity and safety. Noise reduction technology can make a compressor more suitable for operations nestled in residential areas or in enclosed spaces. Evaluating noise level specifications during the procurement process is imperative to ensure the compressor meets operational requirements without contributing to auditory overload.
Much to consider include:
- Db Ratings: Check the official sound ratings; the lower the decibel, the lesser the noise.
- Operational Design: Design engineers often produce low-noise models that can run quietly while still offering ranked performance.
Reliable air compressors tend to be faction-proof; therefore, considering most of these features will help mitigate risks of performance droop.
Identifying Reliable Brands
Identifying reliable brands of air compressors significantly impacts one's purchasing decision. Reliable brands embody quality and durability, which can translate into better performance and longer service life, reducing the frequency of replacements. The consideration of brands can save potential buyers from future headaches related to inefficient, unreliable machinery. This section delves into two critical factors when assessing a brand: its reputation and customer ratings.
Reputation and History
When it comes to air compressors, reputation plays a crucial role in determining reliability. Established brands often have a storied history of producing consistent and trustworthy products. A company with years of experience, like Ingersoll Rand or Atlas Copco, usually indicates a strong focus on research and development, which improves product reliability.
A brand's history can also reflect its ability to innovate. Look for brands that introduce new technologies or improve existing products. Familiarity within the market often outweighs novelty. Evaluate their documented performance over time as well. If a brand has a long history of satisfied customers, it is likelier to stand the test of time and quality.
Consider industry awards and third-party evaluations, as well. ISO certifications and engine certifications, for instance, can speak to manufacturing excellence.
Customer Reviews and Ratings
Customer reviews provide a candid insight into product performance. Potential buyers are encouraged to read multiple reviews across various platforms, such as Reddit, Facebook, or specialized machinery review sites. Pay attention to trends within those reviews. It is common for consumers to highlight issues or successes. Look beyond star ratings to understand specific pros and cons outlined by users.
Maintenance Practices for Reliability
Maintaining the reliability of air compressors is critical not just in extending their lifespan, but also in ensuring optimal performance. Well-maintained compressors are less likely to break down and can work efficiently across various applications. This section will detail key maintenance practices to enhance the reliability of air compressors, discussing the vital components such as routine inspections, lubrication techniques, and air quality filtration.
Routine Inspections
Routine inspecitons of air compressors are essential to keep them operational and reliable. Without effective inspections, issues may linger unnoticed, leading to potential malfunctions.
- Scheduling Inspections: Regular inspections should be part of the compressor maintenance calendar. These checks can help identify any early signs of wear and tear or other complications.
- Checking for Visuable Damage: Inspecting for external damage, loose components, and any abnormal noises can prevent small issues from evolving into significant concerns.
- Evaluating Performance Metrics: Measure key performance indicators such as pressure and airflow. If these parameters fall below expected levels, further investigation is needed.
- Recording Findings: Documenting the results of inspections can create an evidence trail. This record is useful for future reference or repair needs.
Lubrication Techniques
Proper lubrication plays a key role in maintaining an air compressor's efficiency and reducing the notion of wear.
- Choosing the Right Lubricant: Select a lubricant that not only conforms to the manufacturer's specification but also adapts to the working environment. Synthetic oils may significantly enhance performance in high-stress applications.
- Maintaining Lubrication Schedules: Establish a lubricant application schedule to ensure all moving parts function optimally. Schedule regular lube changes, as per the manufacturer's recommendations, to avoid gum and sludge buildup.
- Monitoring Oil Levels: Regularly check oil levels to ensure they are within specified limits. Low oil levels can cause overspeed, overheating, even complete failure
Filters and Air Quality
The effectiveness of air filters significantly influences the quality of operations. Dull filters can impede airflow, causing compressors to work harder and inevitably suffer from thermal-related problems.
- Replacing Filters Regularly: Itβs essential to establish a filter replacement schedule based on usage and atmospheric considerations. Dirty filters need to be replaced promptly to maintain efficiency.
- Evaluating Filter Quality: Not all filters are created equal. Opt for high-efficiency particulate air (HEPA) filters or other types that best serve your compressor's purpose.
- Monitoring Air Quality: Ensure the compressed air meets necessary quality standards, as contaminated air can damage tools, products, and ultimately compromise productivity. Quality control is paramount.
Common Issues with Air Compressors
Understanding common problems that arise with air compressors is key to ensuring long-term reliability. These issues can cause neither only the compressor to malfunction but also impact interconnected systems and tools efficiency. Recognizing these problems can help with proactive maintenance and minimization of operational disruptions. Here, we will discuss two major common issues that may occur: overheating problems and leakage analysis.
Overheating Problems
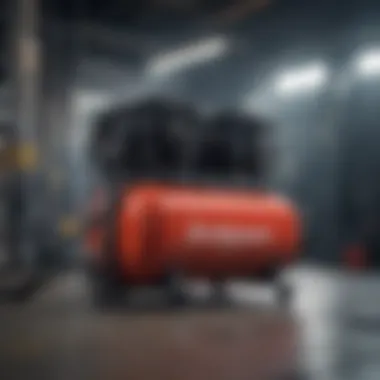
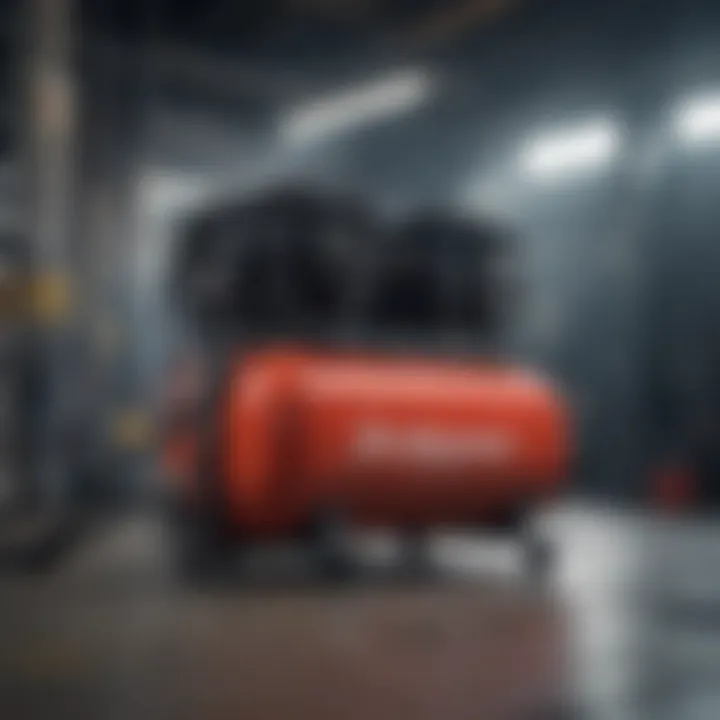
Overheating is a prevalent issue with air compressors. It typically occurs due to several stress factors that can significantly affect their performance and lifespan.
Causes of Overheating
- Insufficient Cooling: Air compressors have cooling systems in place. If these systems work poorly or fail, overheating arises.
- Poor Ventilation: Compressors require ample space for air circulation. Installing them in closed or cramped locations increases the risk of heat buildup.
- Overloading: Constantly pushing the compressor beyond its capacity can create excess strain. This results in higher temperatures.
Consequences of Overheating
Overheating can lead to severe impacts:
- Component Damage: Critical components can fail due to thermal stress, significantly shooting up repair costs.
- Operational Downtime: Breakdowns from overheating result in project delays and potential loss of revenue.
- Safety Hazards: Extremely high temperatures can lead to combustion in worst-case scenarios.
To combat overheating, regular checks on coolant levels and maintenance of ventilation systems are critical.
Leakage Analysis
Leakages can dramatically affect the performance and efficiency of air compressors. Identifying and addressing leaks early can save valuable resources.
Root Causes of Leaks
Leaks often occur in sealed areas, resulting from:
- Worn Seals and Gaskets: Over time, these parts degrade, leading to pressure losses.
- Corrosion: Rust can form, particularly in older models, resulting in holes and cracks.
- Poor Installation: Incorrect setups can create weak spots that lead to leaks over time.
Effects of Leakage
- Increased Operational Costs: Compressor work harder to compensate for lost air, leading to heightened energy expenses.
- Reduced Performance: A leakage directly impacts pressure levels, hindering the tool or application connected.
- Environmental Impacts: Continuous leaks might release harmful substances, contributing to wastage.
To summarize, proper maintenance and monitoring ensure air compressors function optimally. Proactive management of overheating and leakage can enhance overall efficiency, providing substantial benefits for industrial and individual applications.
Future Trends in Air Compressor Technology
The realm of air compressor technology is continually evolving, guided by innovations that promise not only enhancements in functionality but also substantial economic and environmental benefits. Staying abreast of these trends is vital for businesses and individuals that rely heavily on compressor efficiency. Understanding future trends allows potential buyers and operational managers to make better decisions that directly impact efficiency and effectiveness in operations.
Advancements in Energy Efficiency
Energy efficiency remains at the forefront of air compressor technology developments. This facet has gained significant attention as it's linked to both reduced operational costs and minimized environmental impact. Manufacturers are pushing towards compressors that utilize less power while still providing high output.
- Variable Speed Drives (VSD): These systems allow the compressor to adjust its power output according to the demand at any given moment. This feature reduces energy consumption considerably, ensuring compressors do not run excessively when not needed.
- High-Efficiency Motors: Integrating better motor designs often leads to less energy wasted as heat. This means that not only does the compressor perform better, but your electric bill may significantly decrease.
Investing in these energy-efficient technologies proves beneficial not merely for immediate savings but in promoting sustainability, a valuable aspect for any modern organization.
Integration of Smart Technology
Thenext trend is the growing implementation of smart technologies in air compressors. The advent of IoT (Internet of Things) heralds a new age for air compressor functionality and usability. With smart systems, operating and monitoring compressors becomes more straightforward and efficient.
- Remote Monitoring: Users can receive real-time data on compressor performance from miles away, allowing for prompt responses to any issues detected. This means optimal uptime can be maintained efficiently.
- Predictive Maintenance: Advanced algorithms monitor compressor operating patterns, predicting when maintenance should occur. Instead of reactive approaches to repairs, this trend accentuates the emphasis on preventive care, reducing breakdown incidents.
βIncorporating smart technology can profoundly enhance operational continuity, ensuring that every component of the air compressor works at peak performance.β
By acknowledging and adapting to these emerging constructs, strategic advantages can be attained in the marketplace. Reliability in air compressors increasingly ties in with modernization and tech-compatibility, proving crucial for users in dynamic industrial sectors.
Culmination
In this article, the concept of reliability of air compressors has been essential. Understanding the intricacies of compressor types, overall maintenance, and technological advancements influences decision-making effectively. The findings are vital not just for industry professionals but for consumers seeking to make informed purchases.
Recap of Key Factors Influencing Reliability
Reliability in air compressors depends on various factors:
- Motor Power and Efficiency: Higher efficiency often means lower operational costs, implying that investing in power can reduce future headaches.
- Tank Size and Design: The tank's size affects the compressor's performance capabilities and can lead to more stable air pressure.
- Pressure Control Systems: Well-regulated systems often prevent overpressure situations, which can lead to wear and harm.
- Maintenance Practices: Regular maintenance cannot be understated. Following practices such as inspections and proper lubrication is paramount to prevent unexpected failures.
Having a deep understanding of these elements allows individuals to make educated responses to compressor investment questions.
Final Thoughts on Selecting the Right Compressor
Selecting the perfect air compressor requires deliberate evaluation. Focus on:
- Application Needs: Know what you need the compressor for. Different applications might deserve specific compressor types.
- Brand Reputation: Go for brands which have stood the test of time and maintained goodwill in the market. Check genuine reviews thoroughly to authentically get the user insight.
- Feature Financing: Sometimes, not all features seem essential for home use. Prioritization is based on the intended gradations and economical limits.
Ultimately, the path to discerning the right air compressor includes attention to user needs, brand reputation, and feature balance. Understanding these basics can heightsen your overall performance while minimizing issues in air compression tasks.